20161206:
Vor einer Weile hatte ich ein Problem mit meinem anlten 3D-Drucker. Auf der Platine hat sich scheinbar der Eingang für den Temperatursensor im Hotend (Düse aus der der Kunststoff austritt) verabschiedet. Die angezeigten Temperaturen sind falsch und somit spinnt auch die Temperaturregelung. Da momentan keine Ersatzteile bei GermanRepRap vorrätig sind und das wohl bis Mitte Dezember so bleibt, hab ich mir einen neuen Drucker bestellt. Diesmal allerdings einen Bausatz und kein 95%-Fertiggerät. Es wurde ein Prusa i3 Nachbau von Anet, einen „Anet A8“.
20161209:
Der Anet A8 kommt als Bausatz verpackt in übersichtlichen Styroporprofilen. Wenn man direkt aus China bestellt kann man noch mal einpaar Euro sparen, aber hat längere Wartezeit und das gesparte Geld könnte der Zoll verlangen. Deshalb hab ich mich für einen Händler entschieden, der aus Deutschland versendet. Hier der ebay-Link. Bei den Prusa-Klonen gibt es schlechte und weniger schlechte -Auf den Bildern des Händlers ist ein Standard Prusa zu sehen. Bei den Bewertungen und in der Anleitung steht, dass es sich um einen Anet A8 handelt. Also einen der besseren i3-Klone.
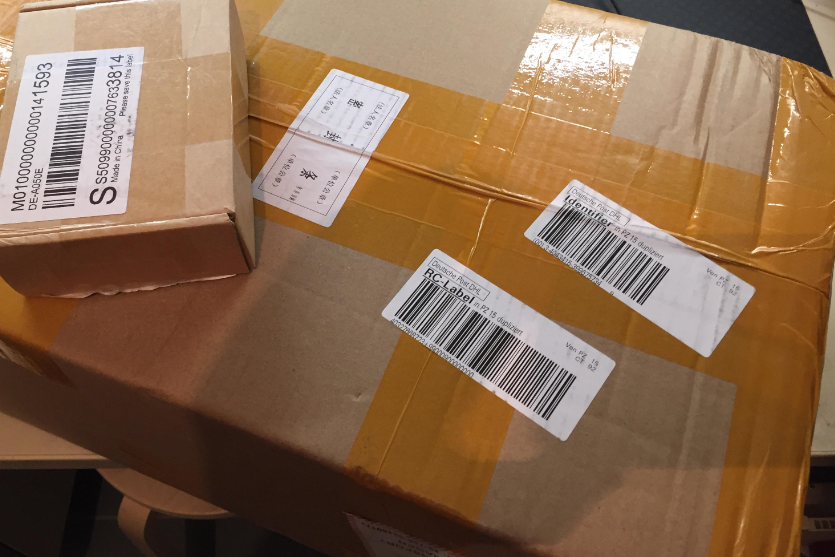
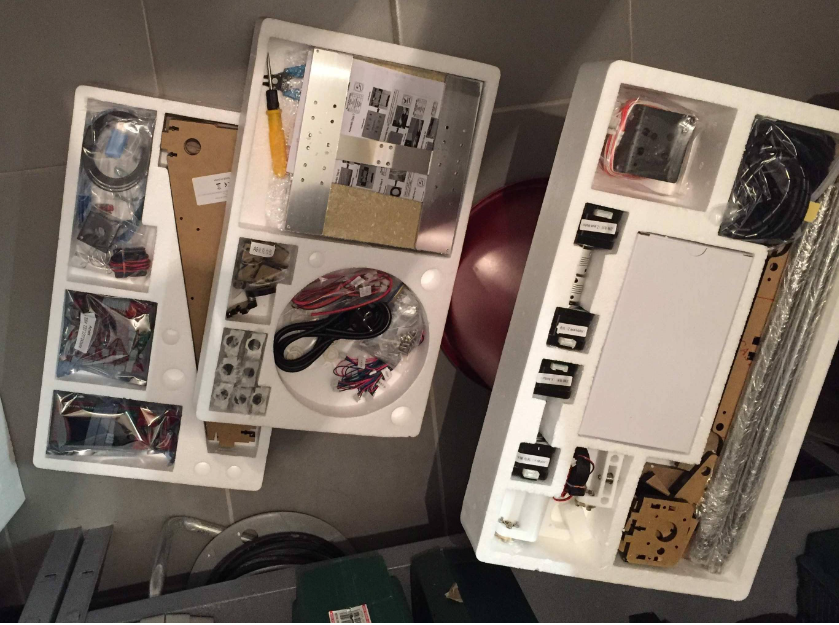
Vorher hab ich mir ein paar Sachen über die Prusas durchgelesen um schon mal vorab Optimierungsbedarf zu definieren. Was mir auch nicht gefällt sind die Extruder, bei denen der Schrittmotor für die Filamentzuführung direkt über dem Hotend sitzt. Mir sind Extruder mit Bowdenzuführung lieber, weil der Schrittmotor nicht auf einem beweglichen Teil sitzt und somit die Gewichtsbelastung viel geringer ist.
Hier mal der Unterschied zwischen den beiden Prinzipien:
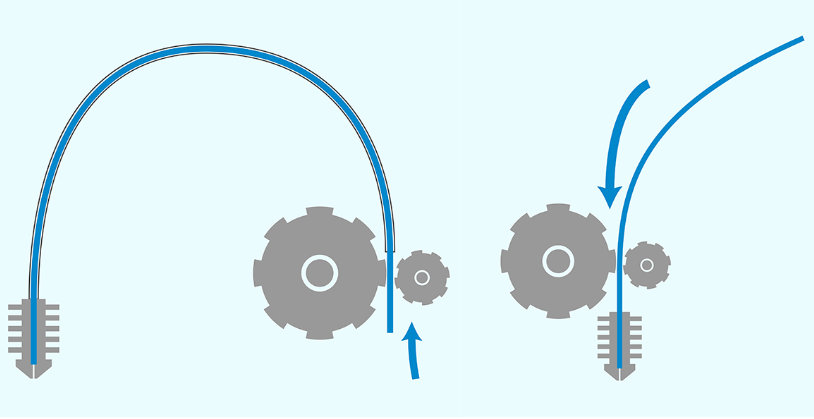
Beim Bowdenzug wird das Filament durch einen Teflonschlauch an die Düse gedrückt. Beide Systeme habe ihre Vor und Nachteile, für mich überwiegen aber die Vorteile des Bowdenprinzips, deshalb werde ich direkt darauf umbauen. Da ich dann natürlich auch ein neues Hotend brauche habe ich direkt ein E3Dv6 mitbestellt. Diese Bauart ist derzeit die beliebteste und servicefreundlichste, wenn es mal zu Verstopfungen oder einem Düsenwechsel kommen sollte.
20161211:
Dann habe ich angefangen das Teil aufzubauen. Zumindest wollte ich das, aber vorher muss man noch die Schutzfolie von den Acrylteilen entfernen. Ich tu mir eh schon bei Aufklebern schwer, also war das absolute Hassarbeit für mich.
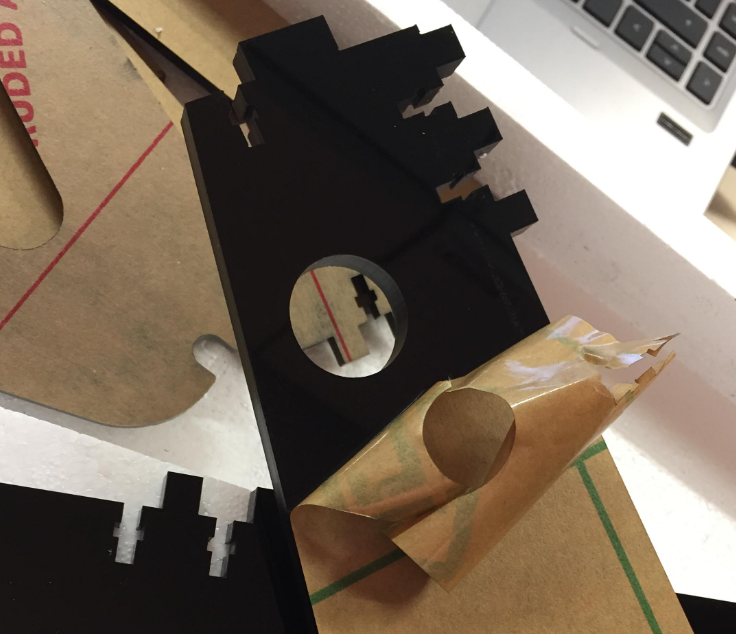
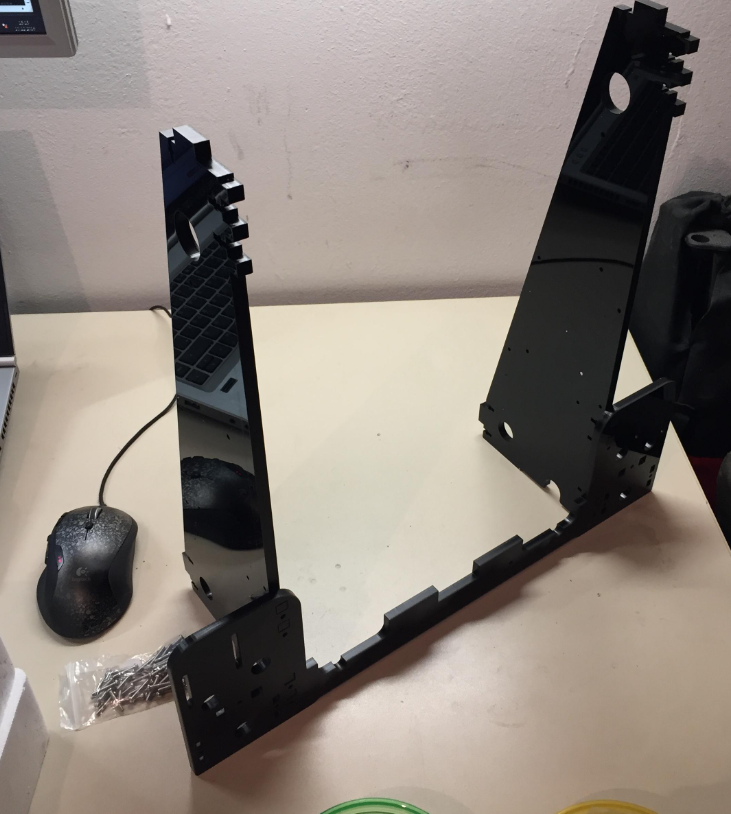
Der Rahmen wird aus den Acrylteilen zusammengesteckt und mit kleinen M3-Schrauben verschraubt, dazu werden M3-Muttern in Aussparungen gesetzt und darin dann die Schraube befestigt. Das sieht etwas komisch aus, hält aber scheinbar.
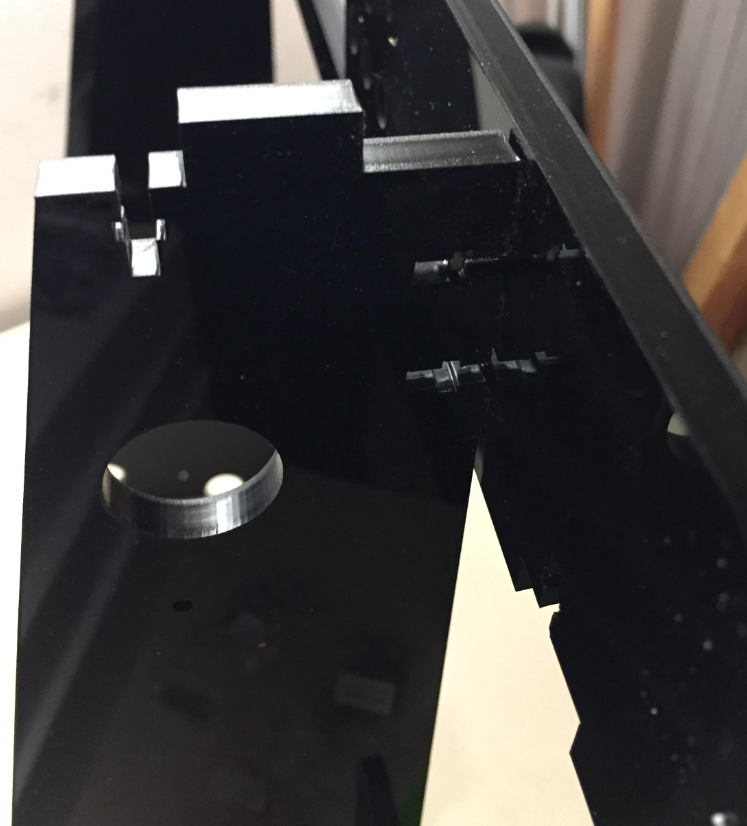
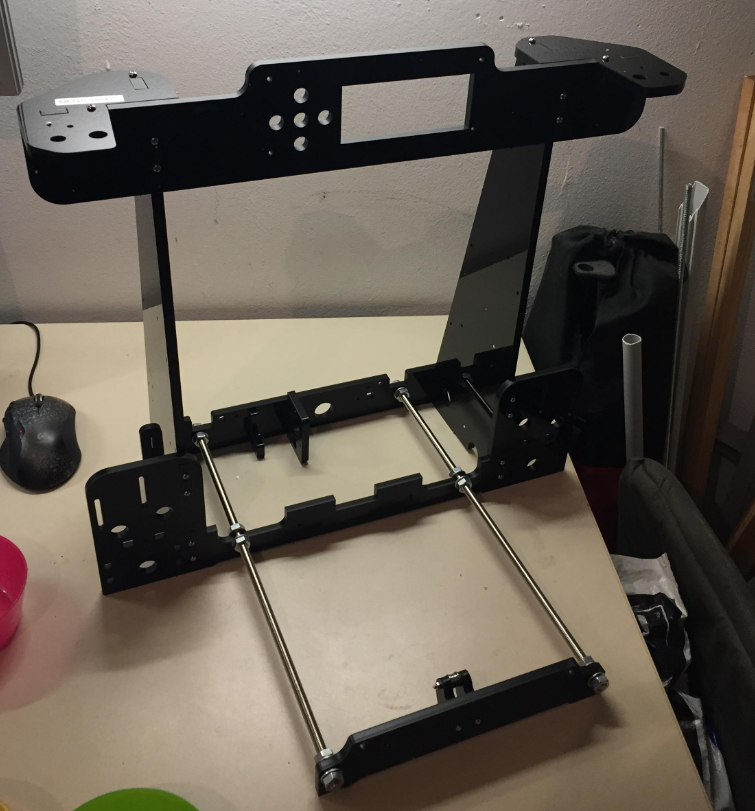
Nach dieser Fleißarbeit steht dann mal der Rahmen und man sieht schon mal wo die Reise hingeht.
Danach geht es an die Mechanik und die bewegten Teile an sich. Die Halterung für den Drucktisch wird mit den Lagerbuchsen auf den 8mm Gleitstangen montiert, Umlenkrollen, Zahnriemen usw. sind alle beim Bausatz dabei. Auf dem folgendem Bild ist auch schon der linke Schrittmotor für die Z-Achse montiert und hinten führt der Schrittmotor für die Y-Achse den Zahnriemen.
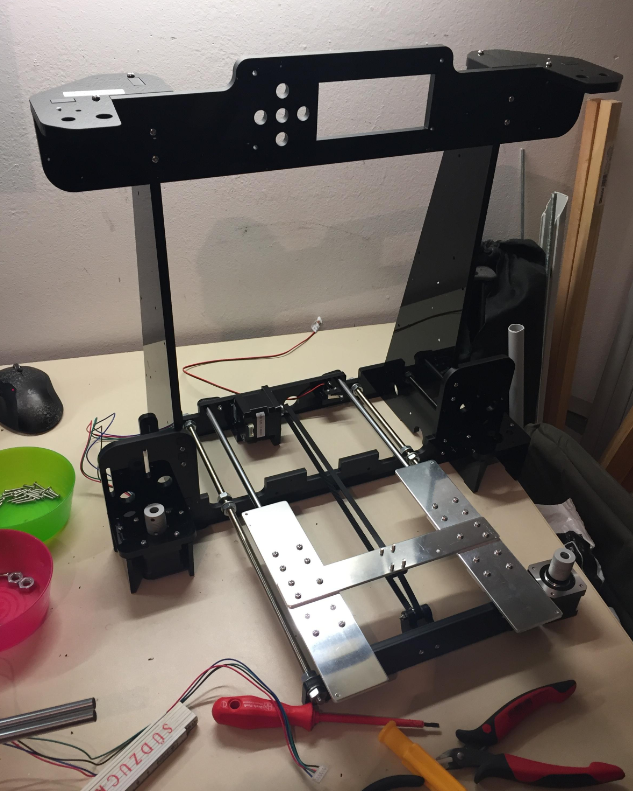
Dann war ich so im Basteltunnel, dass ich keine weiteren Fotos vom aufbau gemacht habe. Erst als ich alles verkabelt hatte hab ich wieder dran gedacht. Die Kabel müssen noch ordentlich in Spiralschlauch gelegt werden (später vielleicht selbstgedruckte Schleppketten), aber wenn man so was zusammengebaut hat, will man auch wissen ob alles klappt.
Ich hatte nicht allzu hohe Erwartungen an die Chinaelektronik, da kommt es ab und zu mal vor, dass Lötstellen nicht sauber sind, oder das ein oder andere Teil nicht funktioniert. Irgendwo muss der Preis ja herkommen. Andererseits funktionierten meine Arduinoklone aus China bisher immer Problemlos, ausser einer, den man an einigen Stellen etwas nachlöten musste. Jetzt aber mal der Moment des ersten Einschaltens – ich war ganz schön gespannt.
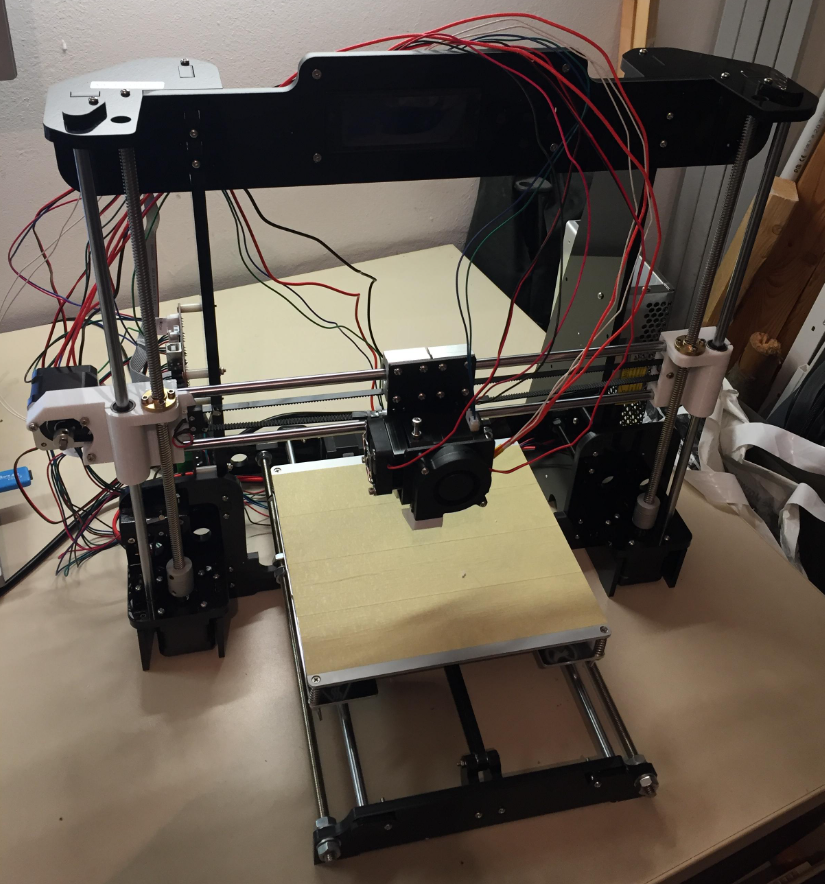
Soweit schon mal gut – ich habe danach noch mal alle Achsen getestet und auch die haben sich bewegt, wie sie sollten. Das Hotend hab ich auch mal kurz heizen lassen, was auch funktionierte. Mehr hab ich erst mal nicht mehr gemacht. Bis jetzt bin ich noch optimistisch und freu mich drauf den Drucker zu optimieren und auch zu nutzen.
Zwischenbilanz nach dem Aufbau:
Es ist schon ne Weile die man braucht. Laut Hersteller zwischen 6 und 8 Stunden. Ich hab jetzt mit Auspacken knapp 5 Stunden gebraucht, aber ungeübte Bastler brauchen sicher die 8 Stunden, da auch keine ordentliche Anleitung dabei ist und man sich auf die PDF-Datei auf der mitgelieferten SD-Karte oder Youtube-Videos verlassen muss. Problem bei den Youtube-Videos ist, dass es sehr viele Prusa i3 Klone gibt und es deshalb ebenso viele Anleitungsvideos gibt. Für Absolute Anfänger ist das Teil daher eher nicht zu empfehlen. Einige mitgelieferte Teile sind mit einem 3D-Drucker erstellt worden, aber deren Qualität ist maximal ausreichend. Die werden im Zuge meiner Umbauten dann durch eigene ersetzt. Die Steuerung der Funktionen über das Display ist nett – aber nicht intuitiv – sobald der am PC hängt brauch ich das eh nicht mehr, von daher verschmerzbar.
20161212:
Das Kabelchaos wurde vorerst mit Hilfe des mitgelieferten Spiralschlauchs beseitigt. So sieht das Ganze doch schon recht ansehnlich aus. Einen Teil werde ich nochmal auf machen müssen, wenn meine Umbauten umgesetzt werden.
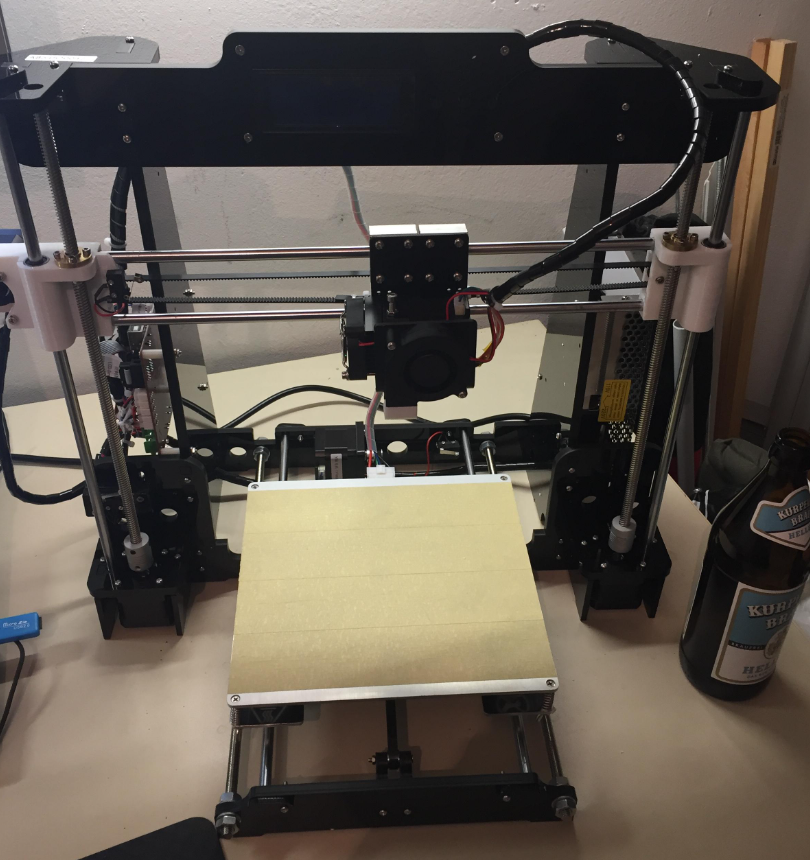
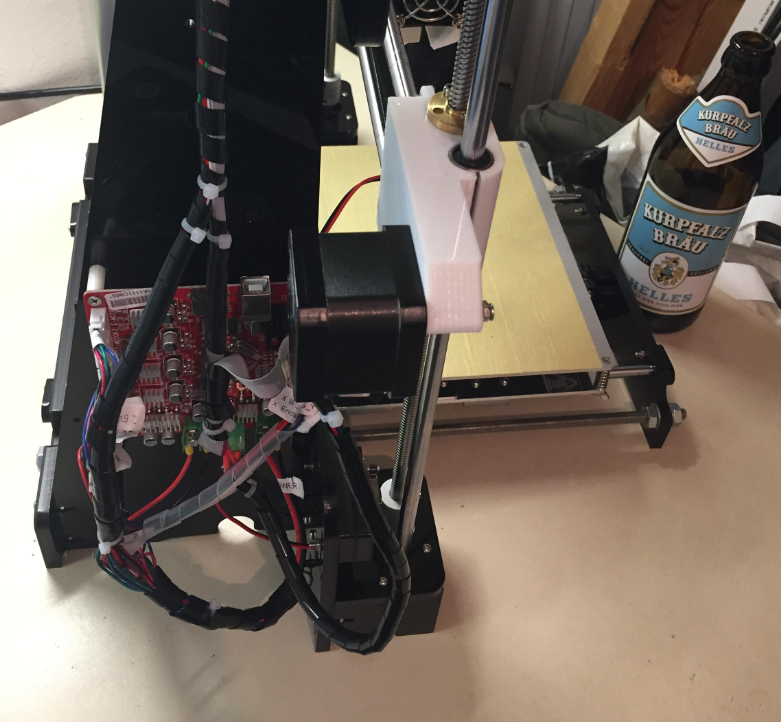
Die Temperaturfühler hab ich auch getestet und die Abweichungen zu meinem Messgerät sind unter 0,5K, was völlig in Ordnung ist. Das Homing der Achsen funktioniert auch schon zuverlässig. Dabei ist mir aufgefallen, dass der Endstop der Z-Achse beschissen einzustellen ist. Der Endstop für die Z-Achse ist deshalb der wichtigste, weil mit dem der anfängliche Abstand von Druckbett zur Düse festgelegt wird. Der Abstand hat Einfluss auf den gesamten Druck, bzw. Die Haftung des Druckobjekts auf dem Druckbett und somit auch die erste Layerhöhe. Eine Faustregel ist, dass man den Abstand von Düse zu Druckbett so einstellen muss, dass man ein normales 80gr/m²-Papier noch durch schieben kann. Momentan ist der Endstopschalter an einer Platte befestigt, die man mit zwei Schrauben und Langlöchern am Rahmen verstellen kann, was nicht sehr genau ist und zudem noch fummelig einzustellen. Da kommt was besseres dran, evtl. was mit Feingewindeschrauben. Evtl. hat das schon mal jemand optimiert und ich kann auf eine druckbare Lösung zurückgreifen. Jetzt muss ich noch ein Profil für den neuen Drucker in der Software anlegen und mal einen Testwürfel drucken. Sobald da was brauchbares rauskommt, fang ich mit den Optimierungen an.
Zwischenbilanz Bausatz
Zum Bausatz selbst kann man sagen, dass alle Teile in erwarteter Qualität vorhanden sind. Schrauben und Muttern sind mehr als genug drin, ich hätte glaube ich noch genug für einen halben weitern Drucker übrig. Leider sind die Schrauben und Muttern nicht sehr hochwertig. Der Spiralschlauch ist auch ca. doppelt so lange, wie man ihn am Ende braucht, aber auch sehr weich. Gute Spiralschläuche sind wesentlich fester und lassen eine gewisse Führung der Kabel zu. Den günstigen Schlauch muss man schon sehr straff wickeln, dass er da bleibt wo er hingehört und nicht an den Kabeln entlang rutscht. Ich hab die einzelnen Segmente mit Kabelbinder fixiert. Die Kabellängen sind auch alle mit reichlich Reserve dimensioniert, so dass es keinerlei Zug auf irgendwelchen Leitungen gibt. Das Netzteil ist ein normales Schaltnetzteil, Ich muss noch eine kleine Box mit einem Schalter drucken, weil es keinen EIN/AUS-Schalter gibt, wenn Stecker drin, dann Drucker an. Den mitgelieferte Spulenhalter hab ich gar nicht aufgebaut, da kommt direkt was eigenes her denk ich. Alles in allem ist der Bausatz wirklich komplett, mit allem, was man braucht um mit dem 3D-Drucken anzufangen – außer das Druckmaterial selbst.Wie dann die Qualität der Ausdrucke sein wird, darauf bin ich selbst mal gespannt.
20161213:
Heute wollte ich den Testwürfel drucken um zu sehen wie sich der Anet A8 so schlägt. Dazu hab ich erst mal in der Software ein neues Profil angelegt. Da ich keine passende Profildatei im Netz finden konnte musste ich mir selbst eine basteln. Dazu hab ich einfach die vom alten Drucker genommen und ausprobiert. Der neue Drucker „versteht“ zum Glück die gleichen Befehle wie der alte NEO, von daher war das kein wirkliches Problem. Vorbereitend habe ich die Z-Achse ausrichten müssen, da die ja links und rechts von jeweils einem Schrittmotor bewegt wird. Um die Z-Achse auszurichten hab ich den Abstand der X-Führungsstangen zu den beiden Y-Führungsstangen gemessen und penibel mit dem Messschieber ausgerichtet. Danach hab ich dann doch die mitgelieferte Spulenhalterung zusammengebaut und eine Restrolle eingehängt und das Filament in den Extruder gefädelt und das erste mal extrudiert.
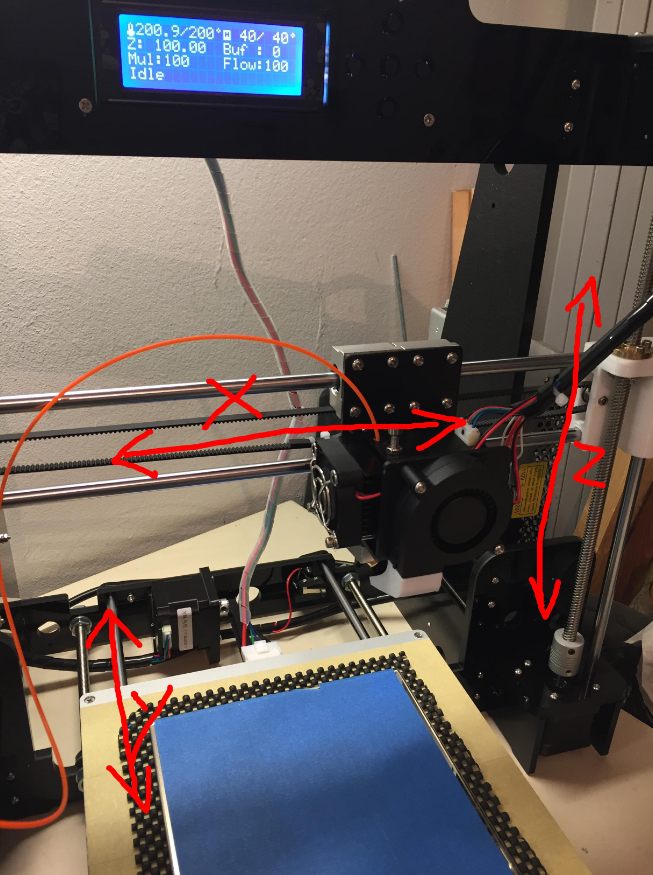
Das extrudierte Würstl hab ich vermessen um den Wert dann in der Software einzutragen. Der gemessene Wert (~0,7mm) ist für die eingebaute 0,4mm-Düse etwas hoch. Gerechnet hätte ich mit ca. 0,45mm. Das muss ich mal beobachten, bei meinem anderen Drucker hab ich eine 0,5mm Düse drin und da kommen ca. 0,55mm dicke Würstl raus. Da ich das Hotend aber e wechseln werde, machte ich mir da erst mal keinen Kopf, sondern richtete das Druckbett aus, so dass in Nullstellung der Z-Achse überall nur noch ein Blatt Papier zwischen Düse und Druckbett passte. Der erste Druck ist ein hohler Würfel mit 20mm Kantenlänge, mit dem man den Drucker erstmal testet. Anhand der Messwerte nach dem Drucken kann man feststellen, wo man noch ein wenig nachstellen muss.
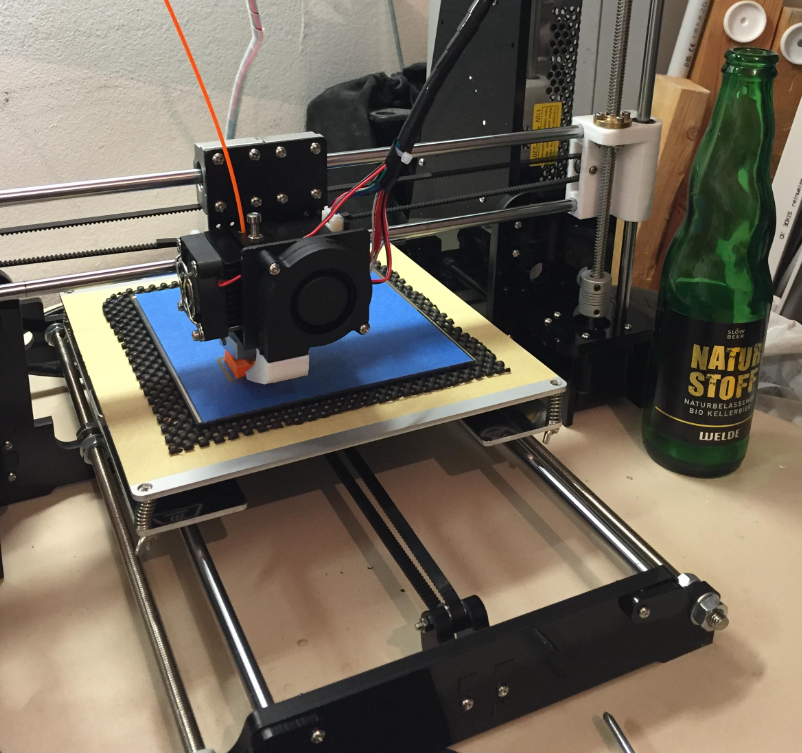
Schwierig für viele Drucker ist bei dem Würfel auch der Deckel – der muss ja in die Luft gedruckt werden, da der Würfel hohl ist. Die ersten Schichten der Oberseite fallen meistens etwas in sich zusammen, aber nach zwei bis drei Schichten sieht das dann gut aus (erkennt man auf dem folgenden Video ein wenig). Die Maßhaltigkeit ist auch schon fast gut. Die Abweichungen gehen sicher noch besser, aber das schiebe ich mal auf die Geschichte mit den 0,7mm nach der Düse.
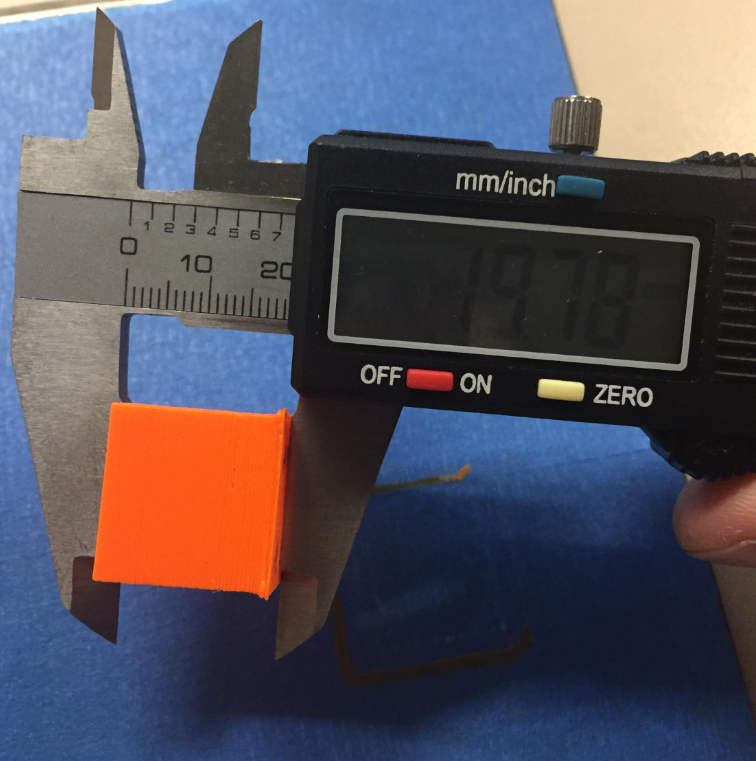
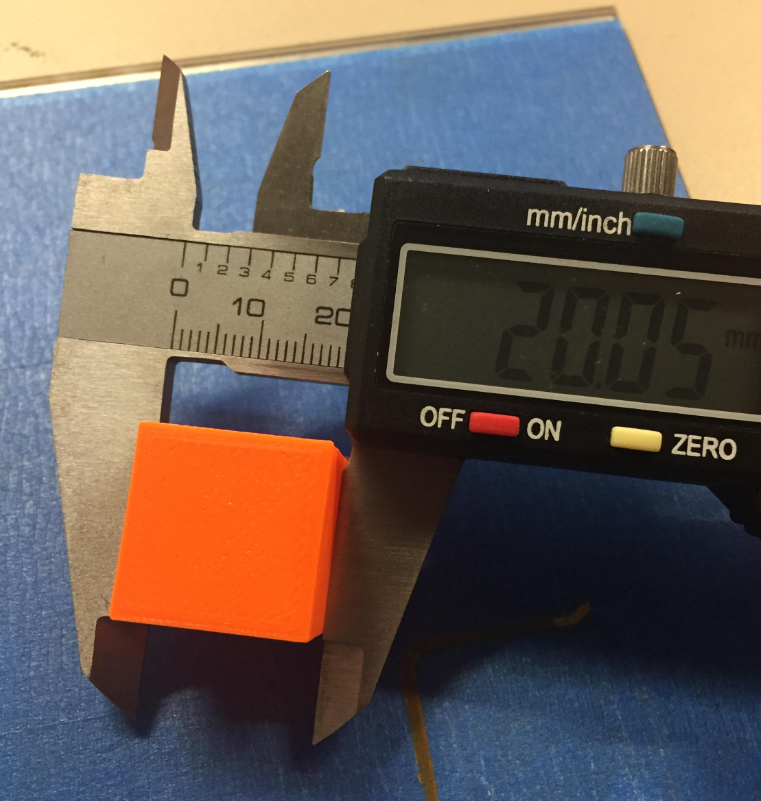
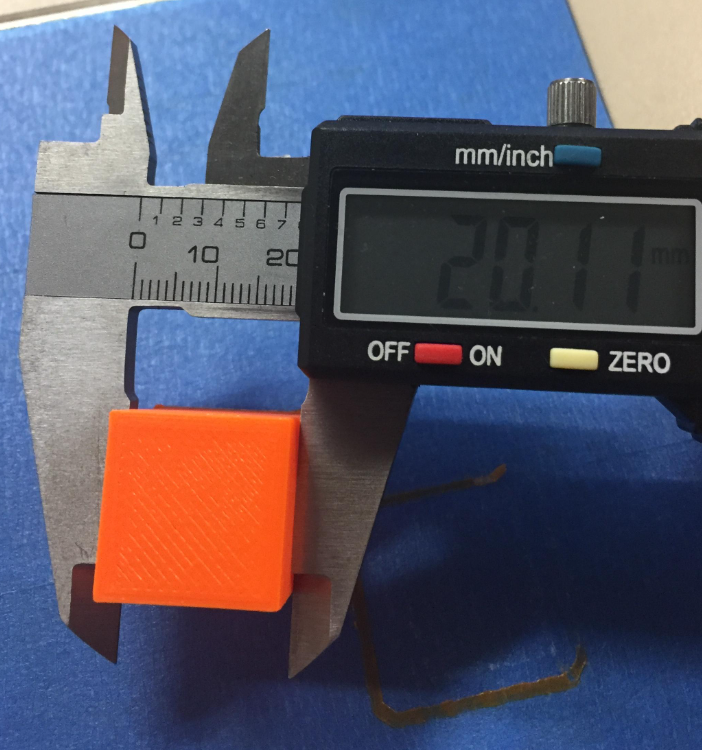
Für den ersten Druck sieht das schon mal sehr gut aus – Die Oberseite ist schön verschlossen, aber an der Vorderseite kam manchmal zu wenig Material nach, deshalb die kleinen Aussetzer. Ich denke, das kam von meiner provisorischen Filamentführung, da das nur bei der X-Achse auftrat und auch nur auf der Seite, bei der die Bewegung der Achse nochmal zusätzlich Zug aufs Filament brachte. Als ich die Filamentschlaufe etwas gelockert hatte waren die Krater ja auch schon fast wieder weg.
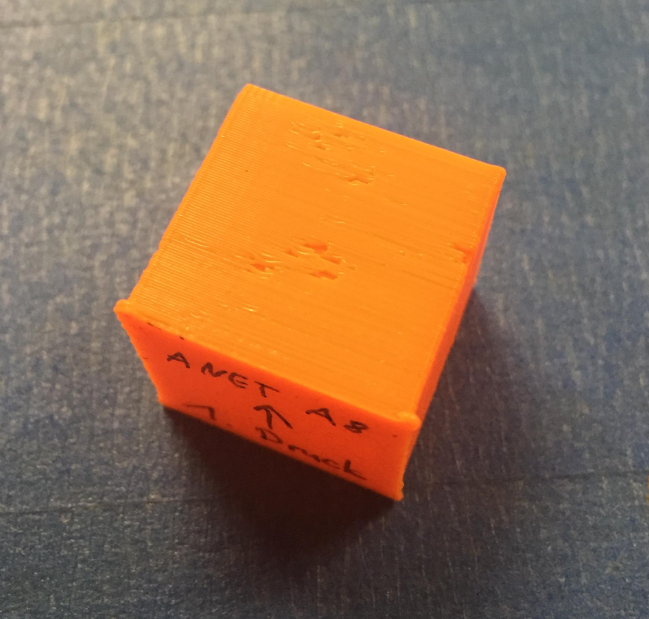
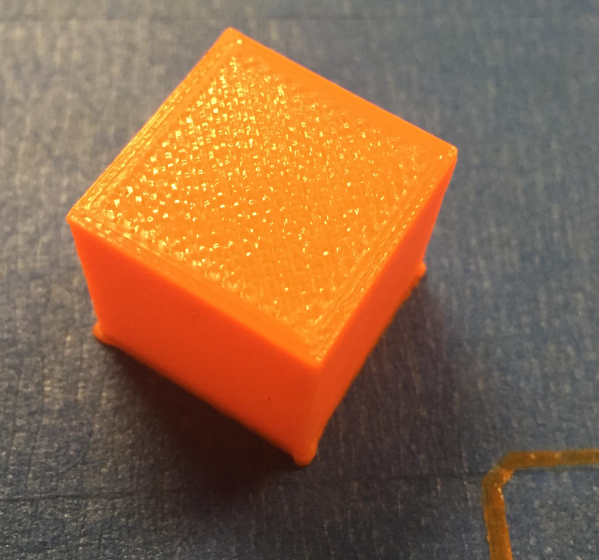
20161218:
Die letzten Tage gings voran mit dem neuen Drucker – allerdings mehr „Prüf- und Einstellarbeiten“ als richtig interessante Punkte. Da ich ja auf Bowden-Extruder umrüsten möchte und mir dazu die Teile selbst drucken will, musste ich doch noch etwas Hirn in die Optimierung der Druckparameter stecken. Die Druckparameter sind einmal Abhängig vom Material, das man druckt (teilweise sind die Chargen eines Herstellers schon unterschiedlich, so dass man neu anpassen muss), von dem Modell, das man druckt, natürlich von den Gegebenheiten des Druckers und den Ansprüchen des Druckerbetreibers. Man muss Geschwindigkeiten der Achsen einstellen, die Fördermenge des Filaments justieren, die Temperaturen ermitteln, bei denen man ein schönes Druckbild erhält und noch einigen Parametern mehr.
Gestartet bin ich mit den Parametern vom alten Drucker, da ich das Material schon auf dem alten Drucker verdruckt habe, kenne ich die Temperaturen dafür schon mal annäherungsweise. Das erste Ergebnis war auch ziemlich gut (siehe auch oben) allerdings hat es auch recht lange gedauert. Ich hab dann mal die Geschwindigkeiten an den neuen Drucker angepasst und nochmal gedruckt. Das Ergebnis war ziemlich ernüchternd. Der Würfel hatte zwar schöne Seiten, allerdings war das „Dach“ nicht geschlossen, weil er da ja eine „Brücke“ ohne Stützstruktur drucken muss, was nicht gelang. Auch der 3. Druck war grottig. Druck 4 sah schon recht ordentlich aus. Dann hab ich mich etwas in ein oder zwei Parametern verrannt und nur noch Mist produziert. Der kleine grüne „Marvin“ sah auch eher aus, als würde er sich das Leben nehmen wollen, wenn er denn könnte. Nachdem ich dann endlich einigermaßen passende Einstellungen gegefunden hatte, hab ich die Teile für den Umbau gedruckt. Dabei musste ich ein vorhandenes Modell eines Bowden-Extruder umdesignen, da ich andere Pushfits verwende wie der Ersteller des Originals. Mehr zu den Änderungen sehr ihr wenn ihr auf dem Link klickt. Ganz zufrieden bin ich mit der Druckqualität noch nicht, aber ich wollte in die „alte Konfiguration“ ja nicht allzu viel Energie reinstecken. Wenn ich mit dem neuen Hotend dann gute Ergebnisse drucke, werde ich alle Teile noch mal neu machen und austauschen.
Ich habe heute noch fast alle billigen Kreuzschlitzschrauben durch gescheite Innensechskantschrauben mit Unterlegscheibe ersetzt, da erstens keine Unterlegscheiben im Bausatz enthalten sind und Das Acryl des Rahmens splittern oder reissen kann, wenn man den Schraubenkopf auf dem Material festdreht und zweitens sind Innensechskantschrauben besser zu „bedienen“.
Auf dem Bild seht ihr mal einen Teil der Drucke die ich zum Testen rausgelassen habe – rechts im Bild liegen die Extruderteile und die neue Halterung für das Hotend.
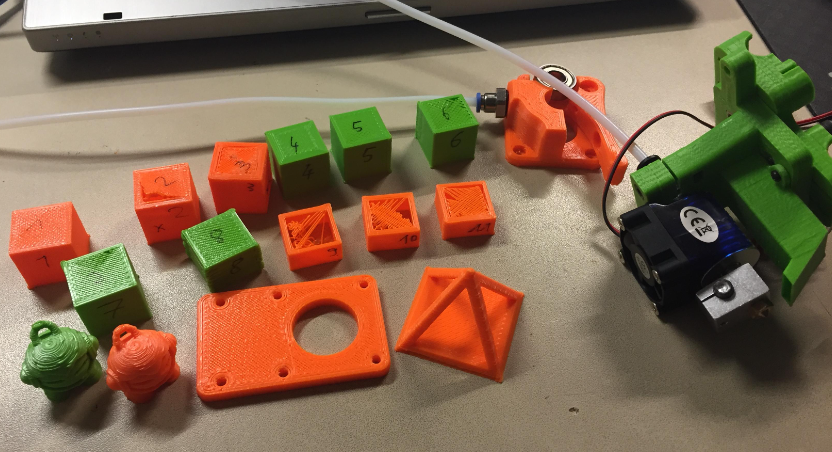
20161225:
Weihnachten ist voll im Gange und während der Rest im Fresskoma liegt, hab ich mal wieder ein paar Punkte aus der (ständig wachsenden) ToDo-Liste abgearbeitet. Diesmal hab ich eine einfache Lösung gefunden, den Riemen der Y-Achse zu spannen. Die Teile hab ich direkt gedruckt und montiert. Mit der dicken gedruckten Schraube kann man einfach die Riemenhalterung nach vorne auf Spannung ziehen.
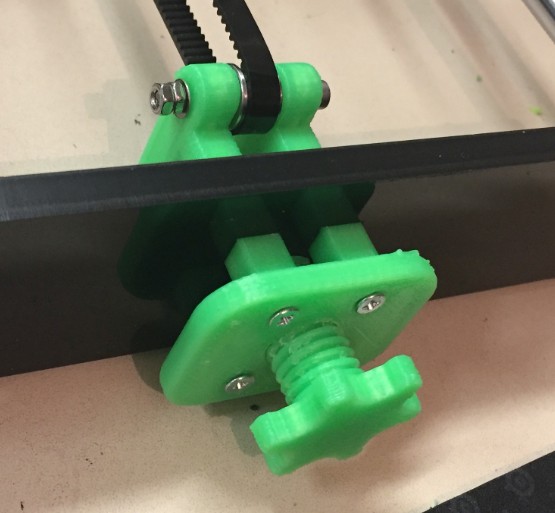
Den anderen Drucker hab ich ja schon vor ner Weile mit einem Raspberry ausgerüstet um das Teil vom Netzwerk aus zu steuern. Das gleiche hab ich jetzt auch beim neuen Drucker umgesetzt, da ich noch einen Raspberry 2 in der Schublade hatte. Da ich das schon im anderen Thread ausgiebig erklärt habe, spar ich mir das hier und versuche mich kurz zu fassen. An den Seitenteilen des Druckers sind mehrere Bohrungen, um verschiedene Mainboards zu montieren. Die zwei Löcher über dem Mainboard hab ich ausgemessen und eine Raspi-Halterung designet, die man da dran schrauben kann.
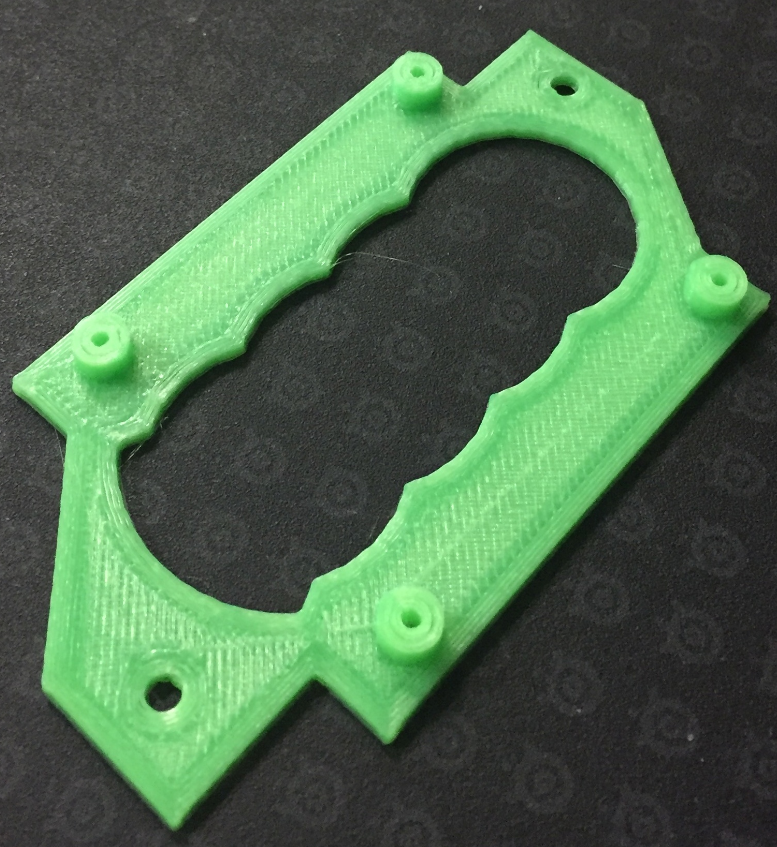
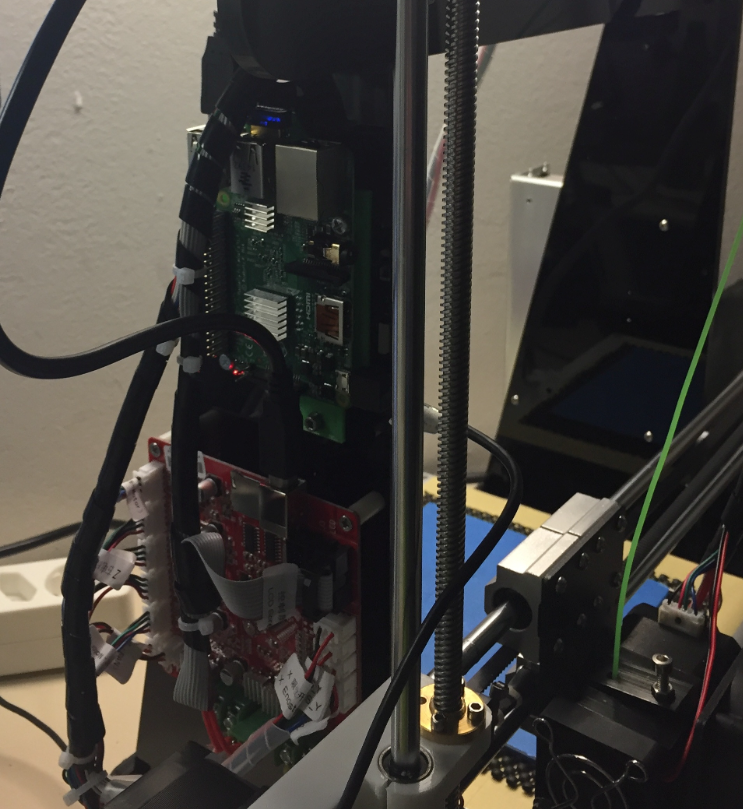
Die erste Variante wurde leider 1cm zu lang – also, falls jemand eine universelle Raspberry-Halterung braucht – ich hätte eine übrig.
Die Spannungsversorgung des Raspberrys wollte ich natürlich auch wieder integrieren und nicht wie viele das machen mit einem zweiten Netzteil unnötig Kabelei am Drucker haben. Dazu hab ich dann auch wieder einen 7805 Spannungsregler genommen, zusammen mit zwei kleinen Kondensatoren und einem Pufferkondensator für die Ausgangsspannung auf ein Stück Streifenrasterplatine gelötet. Kurz getestet und es funktioniert. Auf die Rückseite kommt noch ein kleiner Kühlkörper, da das Teil auf seiner kleinen Fläche ca. 3-5 Watt verbraten muss, als Übergang müssen ein paar große Unterlegscheiben erst mal genügen. Da man die 7805 bis 135°C betreiben kann mach ich mir da keine Sorgen.
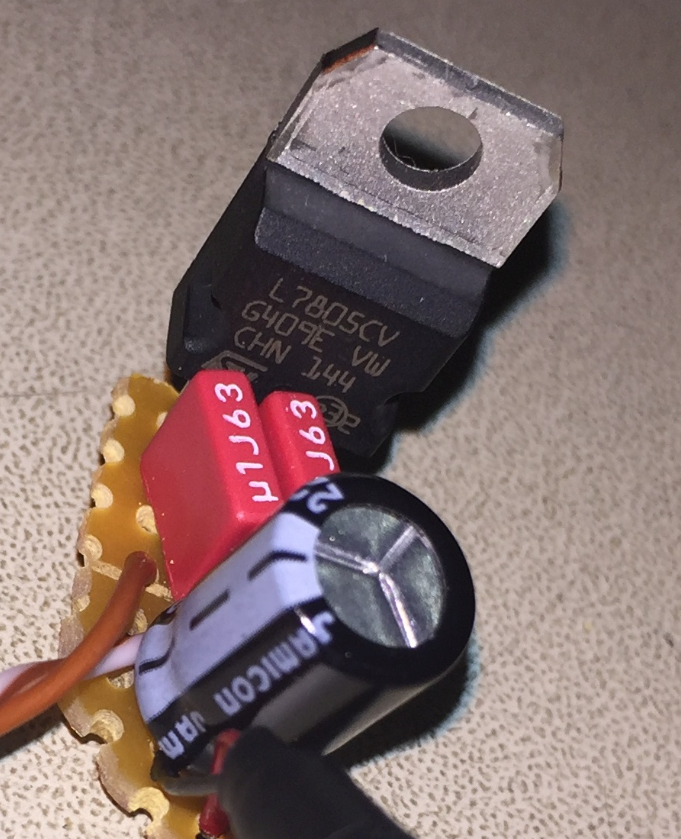
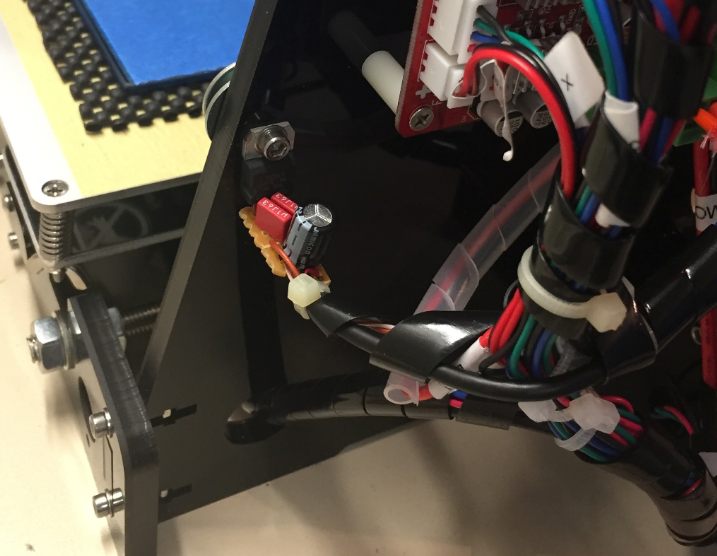
Im Moment läuft der erste Druck über den Raspberry und es sieht aus, als ob alles wunderbar funktioniert.
Was mir tierisch auf die Nerven gehr ist der billige Lüfter, der momentan am Hotend montiert ist, das teil macht einen Krach für zehn. Der kommt sicher nicht ans neue Hotend.
Der andere Drucker ist mittlerweile auch wieder repariert, und bald kann ich dann richtige Vergleiche fahren.
Der Anet bekam noch einige Optimierungen (stabile Siebdruckplatte, Firmwareanpassungen, feingefräste Aluplatte als Druckbett, usw.), wurde aber dann nach vielen Druckstunden verkauft. Für den damaligen Preis und die Verbesserungen ist der Anet ein klasse Gerät. Aber das bessere ist des Guten Feind und die Hersteller schlafen nicht.